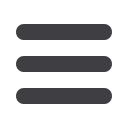
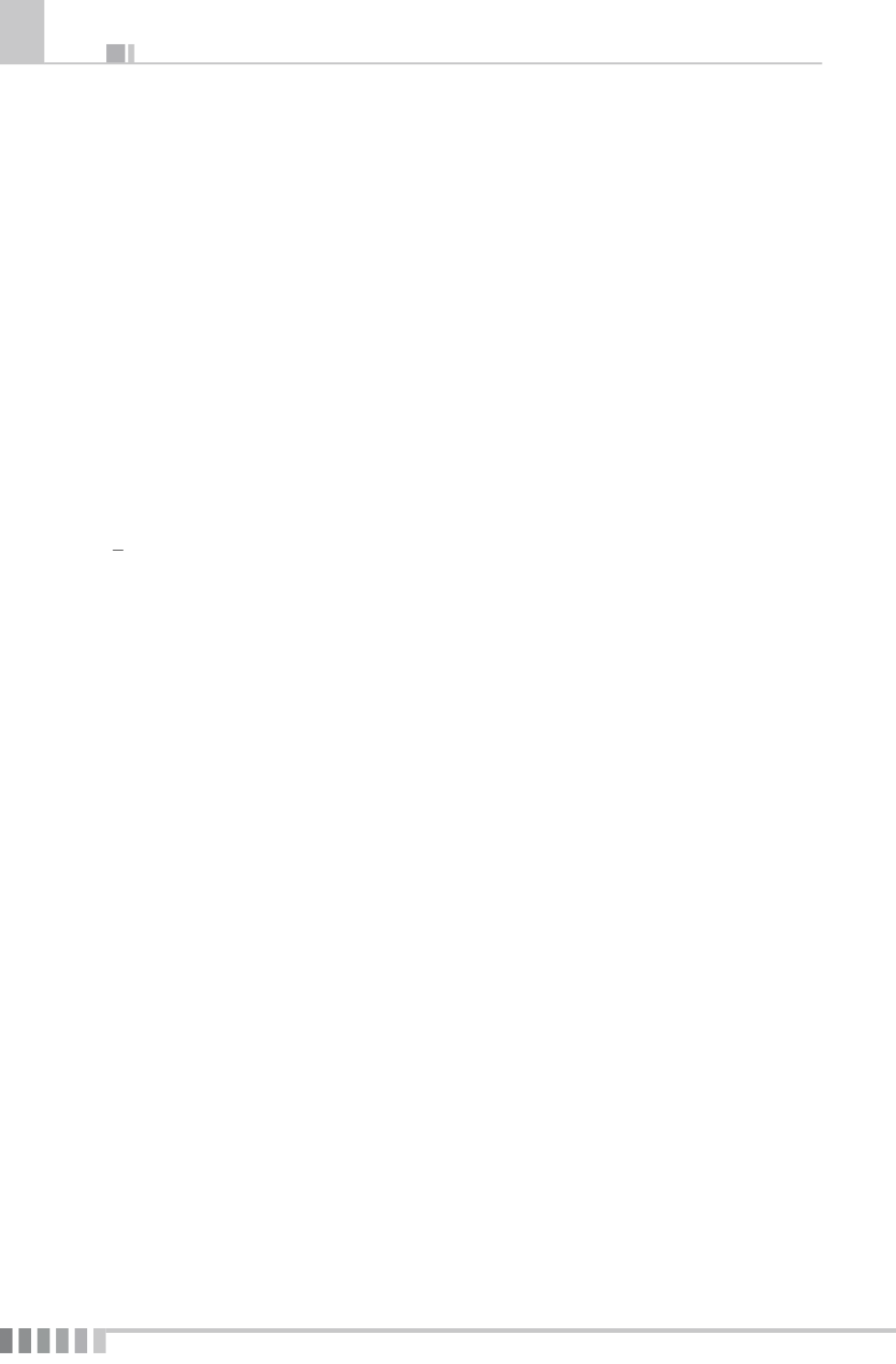
282
Parte Seconda
–
Competenze disciplinari
15) A.
Nel caso di carichi di fatica, il grado di sicurezza di un manufatto
è espresso mediante la probabilità di sopravvivenza o di rottura. Per valu-
tare quest’ultima, è indispensabile disporre delle curve PSN (probabilità P
– ampiezza S – durata N) del materiale, oppure procedere con la sperimenta-
zione diretta di un gran numero di esemplari del manufatto stesso.
16) C.
Se le tensioni residue sono di compressione e normali al piano di
propagazione, possono rallentare, fino ad arrestare del tutto, la propagazione
di una macrocricca.
17) A.
La lappatura è la lavorazione che conferisce la più alta resistenza a
fatica a un organo di macchina, perché, riducendo al minimo le irregolarità
superficiali, incrementa la durata della fase di enucleazione delle cricche di
fatica e, quindi, la durata complessiva dell’organo di macchina. Su provini lap-
pati è in genere eseguita la sperimentazione necessaria alla costruzione delle
curve PSN. Per tener conto della reale finitura superficiale del componente, si
è soliti esprimere la resistenza a fatica attraverso la formula:
S b S
= ,
N
N
2
⋅
con
S
N
resistenza del provino lappato e
b
2
fattore adimensionale che assume
valori via via più piccoli quando dalla lappatura si passa alla rettifica fine e
alla finitura al tornio.
18) A.
All’aumentare del raggio di curvatura del profilo di un intaglio,
diminuisce sia l’effetto di concentrazione delle tensioni sia la sensibilità all’in-
taglio del materiale, con ovvie conseguenze sulla resistenza a fatica.
19) D.
Per i materiali aventi limite di fatica
S
D
(tipicamente gli acciai),
esistono infinite ampiezze di carico in grado di produrre durate infinite: tutte
quelle minori o uguali a
S
D
. Pertanto, la definizione che elimina ogni ambigui-
tà è "la massima ampiezza del carico alterno-simmetrico compatibile con una
durata infinita".
20) C.
La possibilità di determinare un intervallo di ispezione è il principa-
le vantaggio offerto dal dimensionamento alla tollerabilità del danno. Questo
intervallo è dedotto dalla durata del componente difettato, a sua volta valutata
studiando, mediante un modello di
crack-growth
o mediante sperimentazione
diretta, il comportamento sotto i carichi di servizio dei difetti del componente
meccanico. Se
N
i
è l’intervallo di ispezione, espresso in numero di cicli, e
N
f
il numero di cicli impiegato da un difetto per propagare fino a raggiungere la
dimensione critica, si ha:
N
i
=
a
·
N
f
,
con
a
fattore adimensionale, minore di uno, da fissare essenzialmente in funzio-
ne dell’ispezionabilità del componente, della tecnica di controllo che si prevede
di utilizzare nel corso delle ispezioni e, infine, delle conseguenze di eventuali